Tutoriel du 26 novembre 2018
Pourquoi utiliser une caméra thermique ?
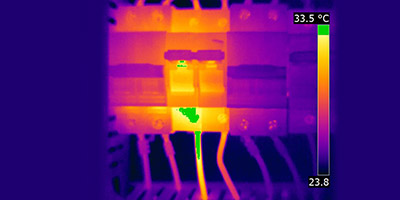
Tout d’abord, avec une caméra thermique qui capte, par imagerie infrarouge, le rayonnement thermique, le technicien peut identifier les échauffements à risque et ainsi limiter les arrêts de la chaîne de production et diminuer le risque humain.
Avec cette caméra, l’électricien peut vérifier les jeux de barres, les sectionneurs, les disjoncteurs mais aussi tous les points de serrages d’une armoire. Aujourd’hui, les assurances ont rendu obligatoires le contrôle thermographique annuel dans leurs contrats surtout pour les sites industriels mais cela ne suffit pas. En effet, lors de ce contrôle, il y a forcément une partie des installations qui ne fonctionnent pas et qui sont de fait non vérifiés. C’est pourquoi il est important de le faire 2 à 3 fois par an afin de palier certaines défaillances dans la maintenance des appareils. Il est préconisé dans une armoire type TGBT de vérifier les serrages des appareils électriques car les micro-vibrations causées par le passage du courant alternatif peut entrainer un desserrement des vis. En ce qui concerne la fréquence de ce type de contrôle, il est généralement conseillé de le faire 1 fois par an tout comme les tests des disjoncteurs différentiels (test recommandé par les constructeurs d’appareils et qui est écrit dans la notice de ce matériel).
Les risques qui en découlent peuvent être dévastateur, on peut aller d’une simple défaillance d’un disjoncteur qui ne tient plus à un départ d’incendie. Dans ces 2 cas, cela peut provoquer des arrêts de production voire d’usine selon l’ampleur et le tableau dans lequel on se trouve. A l’heure ou la productivité est au cœur de la rentabilité, il me semble dommage de prendre de tel risque. Pour les grands sites industriels, il est impossible de faire des campagnes de serrage pour toutes les armoires et coffrets car cela impliquerait un arrêt d’une partie de ses installations et de mobiliser un grand nombre de technicien pendant plusieurs jours. En général on attend les arrêts programmés des chaines ou de l’usine pour effectuer de la maintenance préventive par zone.
C’est pourquoi l’utilisation de la caméra permet de faire une vérification seule, sous tension et rapidement. En plus, sur les nouvelles caméras, il y a 2 capteurs pour prendre 2 images en même temps et le logiciel permet bien souvent de les superposer afin d’identifier au mieux les causes de l’échauffement. Il est important de choisir une caméra avec une résolution de qualité (comme pour un appareil photo) car la précision du point d’échauffement est la clé d’un bon diagnostic. Par exemple, avec une mauvaise image on pourrait croire que le point chaud provient du disjoncteur et donc entraine le remplacement de ce dernier alors qu’en réalité, le problème venait d’un mauvais serrage.